As the central building block in any vacuum system, the design of a vacuum chamber is inextricably linked to the design of the entire system. This which can vary widely, but a vacuum system typically consists of a vacuum pump or pumps, interconnecting piping, viewing window, the central analysis or deposition vacuum chamber, and a variety of other components and devices. All of these depend on the application for which it is used.
The industry, application, and what is being analysed/or deposited in the chamber will underpin the design of a vacuum chamber. Once this has been established the following factors should be considered when designing a vacuum chamber:
Consideration 1: Size and Shape
Vacuum chambers come in a multitude of sizes and shapes with strengths for each. For instance,the world’s largest thermal-vacuum test chamber is housed in the Space Power Facility at NASA Glenn Research Center, measuring at a formidable30 meters in diameter and 36 meters tall. Alternatively, benchtop research chambers (<0.5m3) could be used in small lab environments.
In addition to the size and shape of the chamber a designer would need to consider additional components or systems that the new chamber needs connecting to.
Consideration 2: Vacuum Level
The level of vacuum, whether this is high (10-3 to 10-7 mbar), ultra-high (10-7 to 10-12 mbar) or extreme-high, (<10-12 mbar) will have an overall impact on the chamber design, especially relating to flange type and size. Flanges are used to create an air-tight seal between two components in a vacuum chamber, which prevents air from entering or leaving the chamber. In addition to their sealing function, flanges also provide a way to attach other components to the vacuum chamber, such as vacuum pumps, sensors, and electrical connections.
Flanges
There are two main types of flanges, these are conflat flanges (CF) and Klein flanges (KF).
Conflat flanges
CF typically used for Ultra-high vacuum chambers. CF’s consist of a metal seal and all metal parts, allowing them to be fully bakeable at temperatures up to 450°C. Metal seals, unlike elastomer seals have a low permeation rate, which make them the only material suitable for UHV levels. Copper (must be oxygen free), aluminium and less commonly silver and gold are the most frequently used materials for the seal or otherwise known as gaskets. Silver and gold plated gaskets provide protection from corrosion (flaking) and thus contamination. They can also be baked at higher temperatures, frequently. Therefore, making them ideal for applications that need consistent high temperature bakeouts (such as molecular beam epitaxy (MBE).
CF's can be found in four standard types: fixed blank, rotatable blank, fixed bored and rotatable bored and are normally measured by their outer diameter (OD) in inches. Their sizes can range from 1.33 to 16.50 inches.
Klein flanges
KF are typically used for high vacuum chambers. KF's unlike CF’s do not have a knife edge cut inside the flange in which a seal is created through the metal gasket. Instead, KF use an elastomeric O-ring which is compressed by a clamp that pushes together two mating flanges to create a seal. KF are suitable for applications within low to high ranges of atmospheric pressures and depending on the material used for the O-ring, KF can be baked at a maximum temperature of 180°C.
KF are measured by their inner diameter (ID) in mm. Their sizes can range from 10mm to 50mm.
Consideration 3: Material
There are only a few materials suitable to create the vacuum chamber due to the specific properties required such as density, weight, conductivity, and resistivity.
For many chamber technology manufacturers, stainless steel is the most favoured choice of materials because:
High strength and durability – stainless steel is easily weldable and able to maintain a hermetic seal in extreme high vacuum conditions
High-density – resistant to high and extreme high vacuum
Thermal stability – stainless steel can withstand extremely high temperatures without deforming
Anti-corrosion & cleanliness – stainless steel is easy to clean and sterilize and doesn’t contaminate the vacuum environment making it particularly ideal for semiconductor manufacturing
Magnetic resistance – stainless steel is perfectly suited to applications where magnetic fields are present
- Stainless steel is most suited to achieving ultra-high vacuum
Thermal conductivity – aluminium vacuum chambers have extremely high thermal conductivity rates and very low thermal emissivity rates. Full bakeouts are also achievable at much lower temperatures compared to the likes of stainless steel
Light-weight – from handling, exporting/importing and installation, the lighter load of aluminium material reduces overall costs
Material cost – compared to stainless steel, aluminium chambers are significantly more economical to manufacture
Non-magnetic properties allow aluminium chambers to be used in applications where magnetic fields are present
Consideration 4: Access/Services
Often a large access port on the chamber may be required, for example if an internalcryo shield is needed or an internal vacuum stage. Toenable theintegration of these partsthe use will need a large open flange to fit the items. This may change the design of the that chamberasstrength, magnetic fields will be impacted.
In many cases a dished end will be stronger and lighter, provide better magnetic shielding, and hold focal point tolerances better; but it does not offer the same level of access.
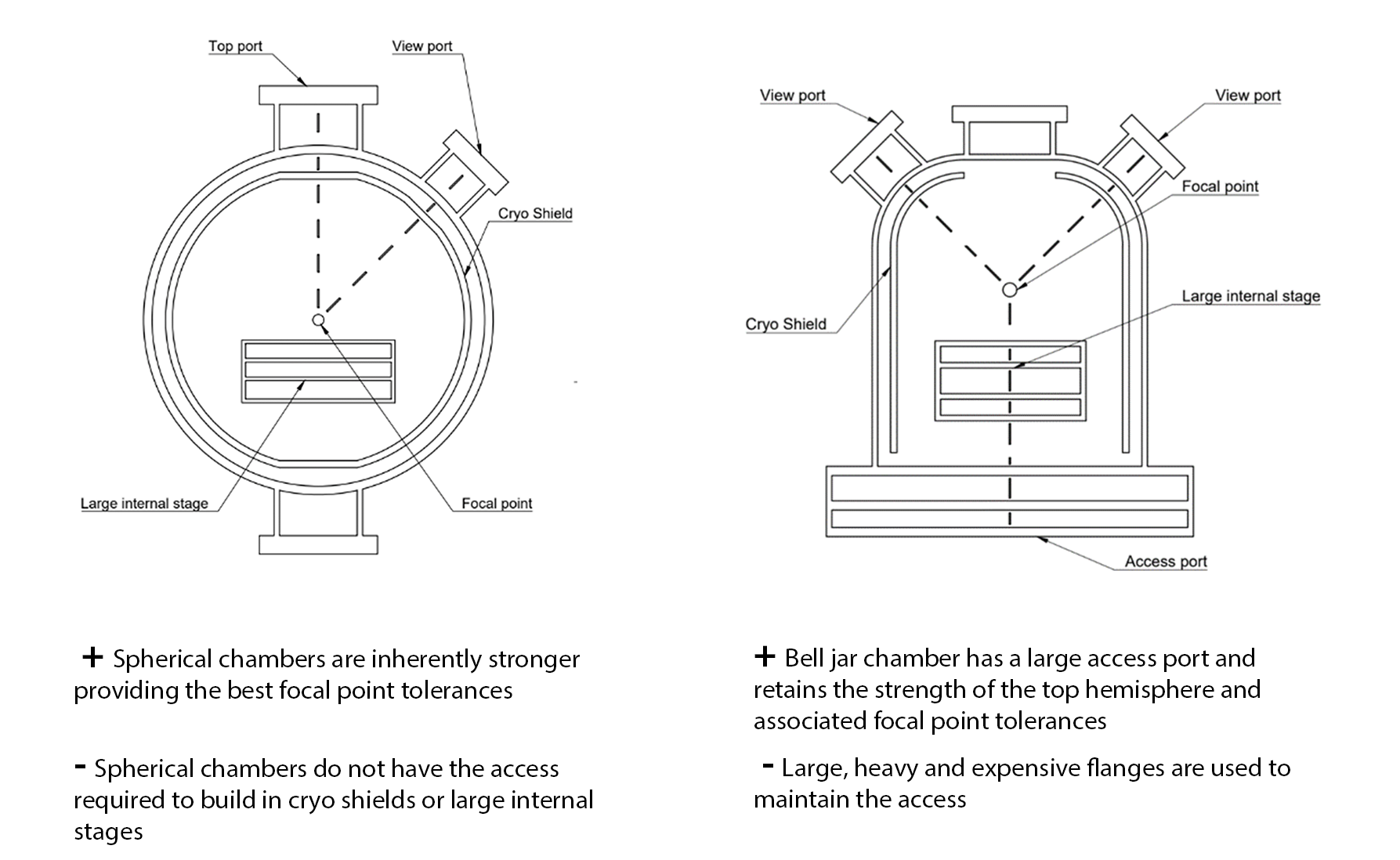
What are the Vacuum Chamber Design Phase Processes?
When it comes to the design phase of chamber technology development, this is typically carried out in one of two ways: the ‘build to print’ method, or the ‘design and build’ approach.
For build to print the customer provides the design for the contract manufacturer to build to.
For design an build the contract manufacturer completes the design element for customer approval prior to the build of the chamber.
By working with a build to print service provider, the customer can be sure that their products will meet the highest standards of quality and performance during the manufacturing process.
The design and build approach Allows the contract manufacturer to build the chamber in the best manufacturable way whilst observing the requirements of the customers experiment.
After discussing the requirements and identifying a solution, the manufacturer will assist in designing and creating the chamber. A couple of key benefits of this process are that manufacturers can assist clients with projects from the very beginning to end, and the responsibility for quality and performance lies with the supplier themselves.
Your High Vacuum Solutions Partner
If you are searching for a certified high vacuum systems’ manufacturing partner for your chamber project, VACGEN make for the ideal partner.
From design to delivery and installation, we have over 50 years of experience in supplying cutting edge high vacuum solutions for some of the most advanced sectors in the world, including: semiconductor, research, aerospace & defence, medical and energy. Get in touch to find out more or to get a quote.